It’s impossible not to notice how much the construction industry has been left behind when it comes to applying revolutionary technology for business development. The construction industry is complex, and there are many variables to consider when trying to understand why it's lagging technologically, and why it can't keep up with the speed at which other fields develop.
46.4% of surveyed construction companies spent less than 1% of their annual sales volumes on IT – JB Knowledge 2017
The 2017 ConTech Survey showed that 46.4% of surveyed construction companies spent less than 1% of their yearly sales volumes on IT. A significant decrease when related to the 55.9% displayed in 2016’s survey. Less than 20% of respondents allocated anything above 2% of their budgets on information technologies.
This is happening because the construction industry has historically been reluctant to pursue improvement through technology. Even though over the last decades we’ve seen considerable upgrades in the delivery strategy of capital projects, construction techniques, and risk management, the construction industry has been left not capitalized on the ability to increase productivity through technological means.
81% of survey respondents plan to spend more on technology in 2018 than what they allocated in 2017 – Software Connect 2017
When you try to look for ways to understand these numbers, you may find something like KPMG’s 2017 Global Construction Survey, where more than 80% of respondents reported confidence in their organization’ ability to deliver projects on time and within budget. You would also see that half of the respondents indicated that adverse project performance had impacted their company.
Nearly 60% of contractors admit that adverse project performance significantly impacted their company in the last three years – KPMG 2017
Could it be that the lack of organisation through appropriate use of technology is what is causing poor project performance?
Is the Construction Industry is Ready to Embrace the IT Revolution?
The construction development industry is undoubtedly going to evolve in the coming years, and as within every industry it’s now more critical than ever to stay ahead of the curve, understanding emerging technologies and what they can do to impact your project management, efficiency and decision making.
In the following analysis, we've brought together statistics from a range of different surveys to help explain:
What the construction industry is doing to gain better access to accurate project data by utilizing digitization and mobile technology.
What the current state of the industry is, what companies are competing against and will be moreso into the future, and how companies can respond to the disadvantages that lagging behind in their use of technology can produce.
How companies can have a head start on the possibilities of upgrading both project management and productivity while reducing costs through efficiently using technology.
This is not just a matter of “If” these technologies revolutionize the industry, but “when” – and the answer to that question is “closer than you may think”.
Nearly 62% of construction companies are experimenting with emerging technology – JB Knowledge 2017
Let’s have a look at the trends surrounding technology that are increasingly affecting the construction industry, including; paperless projects, mobile technologies, drones, automation, Building Information Software (BIM), wearable devices, virtual and augmented reality, cloud-based data management, and more!
1. Walking the road towards paperless construction
McKinsey & Company conducted a study in which it found construction is in the top 3 least digitized sectors when evaluated based on a set of metrics to assess digitization of assets, usage and labor. This is in comparison with 22 other fields such as professional services, oil and gas or media.
By digitization, we refer to the process of moving from paper and manual interpretation and execution of data processing in projects, into more efficient and reliable sources of management that technology allows us to apply, like mobile devices and cloud storage.
40% of construction companies are still using paper plans on the job and nearly 50% of construction professionals manually prepare and process daily reports – JB Knowledge 2016
It’s known that a good proportion of the non-optimal uses of time in construction are related to the use of paper; dealing with physical plans, blueprints, supply-chain orders, daily progress reports, etc. in a time when they could all be fully managed digitally.
Physical information is always going to be shared slowly, and it can even cause mistakes and inefficiencies, due to contractors from different stages of the project having to work based on different iterations of hard copy documents, because they don’t always have quick access to project data digitally.
64% of owners and 77% of contractors use mobile technology in their engineering and construction projects – KPMG 2016
When a company digitizes workflows, it’s almost guaranteed to substantially reduce many hours of staff administratoin time per week; cutting down times invested in making reports and sharing them, boosting productivity, increasing the speed of review and approval of tasks.
All of this being done in a decentralized and connected environment, where information can always be shared digitally in real time.
Nowadays, mobile devices and connectivity are available at low costs; using tablets has allowed the deployment of cloud-based apps that will enable contractors, supervisors and project managers to stay on top of entire projects, any time they need to, without having to deal with the hassle of paper based project management on site.
Within 10 years, full-scale digitization could lead to savings between $0.7-1.2 trillion (13- 21%) in the Design & Engineering and Construction phases and $0.3-0.5 trillion (10-17%) in the Operations phase – WEForum 2016
Having said all of this, we know that we’re not going to escape from paper entirely, but understanding that it is inefficient, and that there’s a lot of room for improvement, is a good start.
2. Usage of Mobile apps
The potential that mobile technology has to increase productivity in the construction industry is something so widely known, that it makes no sense for it not to be the standard in all projects.
For example, construction companies could use mobile technology to improve the flow and management of project data and ensure its accuracy, thereby cutting down on double handling and quality assurance.
On average, 52% of all rework globally is caused by inadequate data and miscommunication – PlanGrid & FMI 2018
One example of mobile implementation has been the usage of mobile apps to replace the so-called “yellow book” where field inspectors would manually report project activities and unresolved issues. Nowadays all of this can be done by inspectors connected to a centralized cloud system from their mobile devices, allowing them to give or take instant feedback from other contractors, and allowing project managers to clearly track and analyze updated project data.
Even though mobile devices provide a considerable advantage, using this technology on site still has its challenges, and that’s one of the reasons why about a third of construction firms have not yet taken advantage of this technology.
75% of surveyed contractors and subcontractors provide mobile devices to project managers and field supervisors, but only 18% of them used apps to access project data and collaborate – PlanGrid & FMI 2018
Implementing mobile devices in the workplace may not be as easy as it might seem however, and construction companies should have a clear course of action when moving towards its use. The decision to invest in technology should be accompanied by a proper deployment and implementation plan.
3. Drones
You may already know this, but drones have been increasingly adopted by construction companies all over the globe, with approximately 1 in 5 companies using them for site surveys, scans, and map and management of construction sites, helping them to complete tasks much faster and more cost effectively than through using other methods of surveying.
18% of small and midsize construction companies use drones, and 26% are expected to be using them by 2020 – Software Connect 2017
The only reason why many companies hadn't adopted drones until last year was the lack of precision of their readings. Nowadays however, their technology has developed rapidly, and every day they’re more advanced, accurate, efficient, less expensive, and automation has allowed them to require much less human involvement to make them work well.
Goldman Sachs conducted a study in which it estimated that the construction industry will be the fastest adopter of drone usage in the next couple of years.
Another proven way in which drones can help increase productivity is using 3D laser mapping or LiDAR to enable autonomous navigation of heavy machinery.
In recent times Komatsu has developed an intelligent machine-control technology; allowing drone surveying, the internet of things, and automation to interconnect machinery and project data collection to complete pre-foundation work almost autonomously.
Something important to remember though, is that just buying a drone isn’t going to increase a company's productivity. They require proper pre-flight planning, settings, post-flight analysis, reporting and data analytics to make data that is useful for enhancing business.
4. Automation is the way to go
Automating workflows is something every company should be aspiring to by the 2020s. Technology has become more streamlined as years pass, and with the computing power we now possess its’ time to think about letting machines do the heavy lifting for us.
11% of surveyed contractors expect estimating and project management workflows to be automated soon – JBKnowledge 2017
24% of construction industry professionals will implement autonomous equipment by 2020 – Software Connect 2017
Automation can completely revolutionize a business. It’s essential however that you understand what “automation” means, and that it won’t completely replace workers anytime soon (and least not in most cases), but will instead be a great tool to enhance their productivity.
Almost 90% of the 500 executives surveyed said they spend 1,300 hours annually trying to organize information from various systems into data they can use – TrackVia 2018
The key to implementing automated solutions is to understand that the simpler your system, the better, there’s no point in utilizing four different automation systems, if they can’t correctly interact and share information with each other automatically. The key is to remove human intervention as much as possible.
Executives that rely on four or more systems to manage their data spend 400% more time trying to use that data for decision-making compared to those who use a single system – TrackVia 2018
Right now, one of the most critical roles automation is filling in the industry is in managing supply chains, enabling tracking of inventory levels and automatically placing replenishment orders for suppliers. This sort of automation can reduce the estimated time of ordering and delivery of project supplies by huge margins. An automated replenishment system could even be equipped with responses to external factors such as market trends or weather factors to optimize prices and delivery times, and any other external factors could be analyzed by software in real time much more efficiently.
68% of executives said they have to make decisions with outdated data – TrackVia 2018
Automation can also allow us to perform advanced analytics on data, and further enhance decision making, identifying possible issues that inspectors could be ignoring for instance. Some other uses of automation in the future could be:
Automated additive construction, or 3D printing
Autonomous navigation technology for construction machinery enabled by LiDAR, and automated vehicles.
Remote-control-free mapping and surveying with drones.
Automated project data management and analysis, reporting, employee time sheets, data back-ups, project updates and more.
By adopting automation technologies, workers would be able to spend less time doing dangerous or strenuous tasks and firms can speed up almost all of their processes.
47% of construction managers still use manual data entry to capture critical data – TrackVia 2018
Inefficiencies in data collection are one of the main issues that are expected to be solved in the coming years through well-implemented automation, increasing productivity, reducing errors in data, and saving in human power.
5. Building Information software (BIM)
One of the leading technologies boosting the efficiency and productivity of the construction industry in the last decade is building information software (BIM), which has helped the industry evolve from simple 2D drawings to rich-data 3D integrated models ready to be analyzed with project management and visualization tools.
By 2025, BIM will have advanced enough in the E&C industry to generate productivity gains of 15% to 25% - BCG 2017
BIM represents a collaborative environment in which international data standards puts a huge amount of detailed project data at the reach of contractors and project managers anytime, anywhere.
51% of contractors currently use BIM software – Software Connect 2017
One of the most impressive qualities of BIM is that it doesn’t just consist of a 3D model of the project, but it could also include other dimensions; like time or costs, to increase the amount of external detail and analysis required, allowing incredibly advanced reporting and tracking.
88% of architects and engineers say that BIM enables better design insight; 74% say BIM tools allow more predictive performance of completed projects; and 67% say that BIM helps teams to achieve the “best possible” design solutions - Connecting Teams 2017
The highest expectations for BIM adoption, is getting entire firms and contractors to work from a single BIM model stored in the cloud, where all project communication can be done in the same digital environment that contains it, integrating all aspects of projects to a degree that’s never seen before.
Most project teams using BIM processes experienced reduced project error (61%); reduced time required for communication (55%); increased client satisfaction (52%), and higher quality projects (52%) – Connecting Teams 2017
BIM doesn’t only help improve project productivity, but it’s also an incredibly efficient way of implementing transparency in companies. Allowing clients to review and get instant feedback on a project’s evolution can avoid countless confrontations, and will likely prevent many uncomfortable and time-wasting meetings.
27% of respondents reported having a dedicated BIM/VDC department – JBKnowledge 2017
As a result of adequately implementing BIM, construction companies can efficiently improve their design processes, improving project tracking and information management, allowing decision makers to make better choices based on more reliable data.
One of the most unsettling aspects of BIM, is that even after knowing all of this, many construction companies haven’t been eager to start utilizing it, as it’s known that implementing BIM requires changes in well-established workflows, practices and procedures, and many companies have an institutionalized aversion to change.
28% of respondents reported that their company does not bid on projects involving BIM, and 25% of respondents indicated that only one or two members were trained to work on BIM projects – JBKnowledge 2017
So should companies invest in updating their workflow to implement BIM? Well, the numbers already speak for themselves, but here is another reason to start working with BIM:
82% of BIM users say they’ve achieved a positive return-on-investment, with another 14 percent breaking even - Connecting Teams 2017
This means that a total of 96% of users have at least made up for the cost of their investment.
6. Internet of Things (IoT)
The Internet of things allows us to install sensors and software to track and monitor all sorts of data from devices that usually didn’t record anything in the past. Performance levels and operating conditions of machinery are just a couple of the benefits we can get from connecting our devices to a network that communicates all project data to a central database.
Wearables can also be implemented on field teams to do much more than counting their steps. Nowadays the construction industry is slowly adopting wearable technology to allow for advanced work tracking; improving safety and productivity levels, minimizing labor waste, and fraud.
The Internet of Things could potentially deliver an economic impact of as much as $100 billion a year by 2025 – MGI 2017
Of course, keeping a vast array of devices interconnected and feeding information opens opportunities to collect a tremendous amount of project data, and the potential for optimization is just as significant. Getting all of the data into a single central database allows project managers to make more intelligent decisions.
Adopting IoT does require finding a way of incorporating all of the data into a single system that can correctly process it to make it advantageous for engineers and project managers, and that’s where IoT has its most significant challenges.
Companies can deploy advanced analytics as the primary way of processing big data in projects, and improve day-to-day decision making, and the precision on estimates of project costs and risks.
Applying advanced analytics of data available from email traffic, drawing revisions, team composition and human resources performance data can lead to productivity improvements of as much as 25 to 30 percent – MGI 2017
The main reasons for IoT being used in the construction industry today are:
Inventory management: Connected systems that can detect when stocks are running low, and automatically order for restocking.
Employee tracking: with wearable devices continually feeding data and location of employees, supervisors can get a closer look into productivity levels that could be optimized.
Equipment monitoring: by using sensors in machinery, repairs can be easily detected instantly as needed, and automated alerts can be sent to maintenance teams.
Structural assessment: IoT is also being used with structural sensors testing reliability on structures during construction stages, allowing them to spot deficiencies and quickly correct them.
7. Virtual and Augmented Reality
Virtual Reality (VR) and Augmented Reality (AR) are technologies that have been making more and more headlines recently. And you might already be aware that they’re starting to be a solid piece of the AEC (architecture, engineering and construction) toolset.
Even though they’re currently being used for different purposes, VR and AR are both making huge improvements to the construction industry, and their impact is going to be increasingly evident in years to come.
One of the primary uses for VR has been in the form of project walkthroughs and employee training programs, and AR is starting to break through as a tool to provide virtual feedback on real-world project progress and virtual collaboration and review.
Of the two, AR has proven to be the most impactful in project development, as allowing interactivity between the real physical project and overlaid virtual elements is a technology that will impact most high-scale projects, and there’s no doubt about it growing exponentially in the following years.
16% of respondents said they expect to be using AR or VR in construction projects before 2020 – Software Connect 2017
Until recently, the main reason for most companies not being ready to adopt VR or AR, had been that the costs were quite prohibitive, and only the more prominent firms were able to implement them due to the requirements for additional tech teams ready to successfully fit the platforms to the company's construction environment.
Even though most project managers in mid or small-sized construction firms might feel like the budget requirements still aren’t that appealing, advancements in these technologies, their popularity, and prices going down have been opening them to broader markets. This is possible due to easily being able to outsource the required VR and AR tasks to more affordable companies both on and offshore.
Another issue VR and AR have had in recent times was their ability to keep up with the chaotic speed requirements for project developing, and only the most competitive firms adopting quick and affordable services can survive in such a demanding environment.
At Render3DQuick, we are proud of our VR and AR services as well as our virtual tour and staging capabilities, with one of the most knowledgeable and experienced teams, we can implement any solutions you may require for your project’s needs.
But what are the benefits of implementing VR or AR, you may ask?
Better project reviews and design representation:
Imagine taking a prospective client or one of the project’s stakeholders through a virtual walkthrough of your building from anywhere in the world in the comfort of their offices, even in your building isn’t built yet.
Talk about instant credibility! Developers clients are able to see what the project will look like, from the very first stages of construction, turning a patch of dirt into a towering commercial building, without the hassle of building in reality. Instantly facilitating their decision-making process without having to go through concepts that can be difficult to fully communicate through 2D drawings and charts.
Improving project safety:
VR can allow inspectors to remotely inspect the construction safely, without having to be exposed to hazardous environments as they often would be, and it would be easier to take experts to problem areas to provide an initial diagnosis without them being exposed.
Another quality of VR is that of providing virtual training to employees in a safe environment, evaluating and improving their instant response capabilities and split-second decision making in dangerous situations.
Improve collaboration capabilities and reduce the costs of rework
There’s a trend in many construction firms requesting virtual walkthroughs within the design stage so that stakeholders, architects, subcontractors and other project decision makers can evaluate the project and design, and can ensure everyone has agreed on the final design before moving onto further stages.
52% of rework is caused by poor project data and miscommunication – PlanGrid & FMI 2018
Going through a virtual representation of the building can provide the opportunity to identify possible issues before they become more significant.
There are many occasions in which a subcontractor didn’t quite understand a requirement they had to meet by looking at the plans, and this is precisely the sort of situations that a VR representation can prevent. Getting the opportunity to reduce rework is always a good thing, in all projects.
Up to 70% of total rework experienced in construction and engineering products are a result of design-induced rework – Quality 2017
If subcontractors can see the expected design outcome in advance, they can easily spot issues or discrepancies in data and design, reducing waste and increasing profit at the same time by removing the need to fix costly mistakes later in the process.
8. Projects on the cloud
The construction industry has been having a massive shift towards cloud software and project data sharing in recent years; this has happened due to the distance and varying requirements of working on many different job sites.
75% of construction companies use cloud storage – CITE Research 2018
There are many applicable benefits for implementing cloud-based integration across multiple project stages, enhancing data sharing capabilities, and reducing the occurrence of various issues that come with file management on large teams.
Cloud-based apps allow time to be saved in unnecessary meetings and the inefficient transmission of ideas via email or other messaging platforms with limited reach across team members.Because of its global reach, cloud-based data sharing is almost an instant go-to for most firms.
Every mobile device in the hands of project supervisors and engineers can be easily connected to the cloud, and allow instant reporting to every project member with the touch of a button, in a matter of seconds.
Given the affordability of adopting this technology, there’s no question about It being mandatory in order to stay competitive in today’s markets.
Roughly 67% percent of IT decision-makers in the construction INDUSTRY believe that both data loss and data security are the primary concerns of using digitization of project data – CITE Research 2018
One of the main setbacks for cloud storage, is that many IT managers in construction are concerned about data loss and data security. The truth is that technology isn’t perfect, it comes with its downsides, and in a world plagued with cyber-attacks, this topic should never be overlooked.
36% of construction industry’s ITDMs in the US say that increasing cybersecurity is their top priority – CITE Research 2018
Fortunately, technology does allow us to be prepared and prevent these problems with careful management, whether it is to establish safe management of data and strong cybersecurity procedures within the companies’ systems, or to ensure safe back up and login techniques like encryption & two-step authentication are used to protect information stored in the cloud.
Our final thoughts on the current state of the construction industry in regards to the adoption of technology
If after reading this article, you are thinking “why hasn’t technology been implemented everywhere in the construction industry?” then we have one of many answers for you:
40% of construction firms say new technology has not been implemented due to lack of support, followed closely by budget concerns at 37% and employee hesitance at 32% - JB Knowledge 2016
To be fair, AEC companies have often shown a poor track record on the adoption of new technologies when compared to other industries. These are the top three reasons why most firms still hesitate when considering increasing their IT budgets, but they all have workarounds as below.
Lack of support requires the proper assignment of an IT dedicated team that can be trained to manage and understand every requirement or needs of field teams and project managers before starting implementation.
Budget concerns will always require a correct analysis and planning of projects, as well as an understanding of the return on investment of implementing technology. Done right, technology adoption pays for itself. Appropriate use of IT will always increase productivity and return positive effects on costs, schedule, and risk optimization.
52% of respondents consider the needs of field staff as a top consideration for investing in technology, but only 28% actually receive feedback from field staff before investing in technology – PlanGrid & FMI 2018
Another reason why technology is adopted inefficiently in the construction industry is the lack of knowledge from field teams on the appropriate ways of increasing their productivity with it.
When field teams don’t receive the right training on new technologies, they end up continuing in old ways of working instead of adopting the technology. Think of the levels of complexity you might not want to add to your workflows, and try implementing intuitive and straightforward technology solutions to encourage their use.
The final question is: Is a company ready to embrace technology?
36% of construction professionals cited the reason technology failed was because of poor fit with current processes and procedures - PlanGrid & FMI 2018
Partnering with technology companies to handle project IT needs is a solution that has been taken advantage of by a huge portion of the industry, where construction companies are able to shift their technological responsibilities to companies who specialize in those areas. This can be a better short-term solution, than training a team, and implementing an IT department in one's own company.
IT implementation doesn’t happen overnight, and we advise anyone reading this to use every bit of data they can to prepare for the changes coming this year and into the future. We also encourage anyone reading to become one of the construction industry’s revolutionary leaders, who adopts new technologies in an efficient, sensible and cost-effective way in order to stay ahead of a rapidly changing industry.
Embracing innovation has allowed countless companies to make huge leaps and gain competitive advantages in every industry, and there is huge opportunity for companies in the construction industry to do the same!
Sources
2017 JBKnowledge ConTech Report
2016 JBKnowledge ConTech Report
2017 Connecting teams – Dodge data and analytics
2016 KPMG - Global construction survey
2017 KPMG - Global construction survey
2018 Plangrid – Construction disconnected
2017 Sana – Construction trends Whitepaper
2016 WEF – Shaping the future of construction
2017 WEF – Shaping the future of construction
2018 WEF – Shaping the future of construction
https://blog.capterra.com/tech-collaboration-in-design-and-build-construction/
https://blog.capterra.com/the-5-most-important-construction-statistics-for-construction-managers/
https://blog.plangrid.com/2018/08/construction-industry-statistics-to-improve-productivity/
https://blog.plangrid.com/2018/06/10-data-driven-construction-strategies-to-boost-productivity/
https://softwareconnect.com/construction/technology-trends-2018-report/
http://www.constructionworld.org/top-10-construction-technology-trends-2018
https://www.detarplus.com/2018/07/09/construction-is-trying-really-to-move-away-from-paper/
https://www.sana-commerce.com/us/blog-us/us-construction-industry-trends/
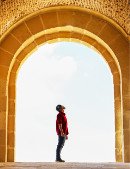
Alex Smith
Manager & Co-Owner Render 3D Quick
Alex Smith is a manager and co-owner at Render3DQuick, with over 6 years’ experience project managing their large team of 3D rendering professionals. Alex is obsessed with architecture and is a CAD design specialist in his own right and an expert in the field of architectural visualization, 3D rendering, and virtual reality tours.
As the first point of contact when you get in touch with Render3DQuick, Alex loves sharing his knowledge and answering any questions you may have about architectural visualization or the latest technologies and techniques they utilize.
Connect with Alex on LinkedIn here.